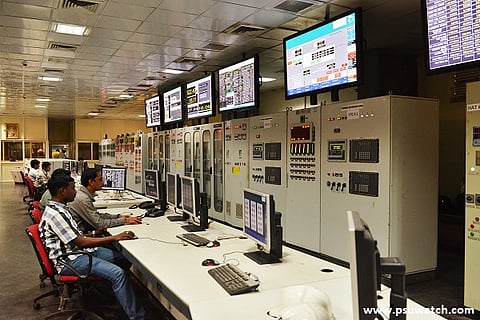
Rourkela: In the calendar year 2019, the Energy Management Department (EMD) of SAIL's Rourkela Steel Plant (RSP) has registered remarkable performance on different aspects. The department was able to accomplish many milestones on account of ISO certification and improvements in techno-economic parameters with regard to energy consumption in the plant.
EMD as a nodal department helped the steel plant to get the global standard ISO 50001: Energy Management System certification for Blast Furnaces – 5, Coke Oven Battery – 6, Power & Blowing Station (PBS) and New Plate Mill departments. In a function organised recently at CEO's conference hall, RSP's CEO Dipak Chattaraj received the prestigious certificate in the presence of Executive Director (Works) PK Dash, Executive Director (P&A) Raj Vir Singh, Executive Director (MM) DK Mohapatra, Executive Director (Projects) Pankaj Kumar, Chief General Manager (F&A) P Nigam and the Departmental Energy officers of the plant.
EMD of RSP also participated in the five-star energy conservation award competition organised by the CII Eastern region in August 2019 and was awarded 4.5 stars in the large scale category.
The EMD collective was instrumental in enhancing the energy efficiency of the plant by undertaking proactive measures. The efforts not only helped in further improving the techno-economic of the plant but also ensured better productivity and savings. The team meticulously analyzed and successfully sorted out the low nitrogen pressure problem being experienced in the coal dust injection (CDI) and pulverised coal injection (PCI) system. The effort led to a savings of 2,000 normal cubic meter of high-pressure nitrogen gas per hour amounting to approximate rupees 1.35 crore per annum. The team also successfully eliminated the problem of venting of steam of about 5-6 ton per hour in PBS. It has led to the enhancement of power generation of PBS by 1-MW approximately. The excess steam from CDCP of coke ovens battery- 6 is now being utilized in the PBS process steam line, thus bringing about a savings of around Rs 4.8 crore per annum.
Besides, the department has also undertaken several other initiatives including providing an alternate nitrogen line to special plate plant to improve nitrogen pressure for the process requirement of the plant. The department also emphasizing upon knowledge and skill retention, has started an intensive learning programme LTTE (Learning Together- Team EMD) where various important topics of the department are discussed and shared amongst the collective.
Disclaimer: This story is a press release and is being published without any editing by PSU Watch desk. Our editorial team has only changed the headline.